Key Regulations and Standards for 500 ml Blood Bags
Overview of International Standards
500 ml blood bags are manufactured and distributed under stringent international norms to ensure quality and safety. Such level of standards ensure the quality of blood products and protect both donors and recipients.
ISO Standards for Blood Bags
The International Organization for Standardization (ISO) provides comprehensive standards that apply to the manufacturing of blood bags. ISO 3826, in particular, is pivotal as it outlines the requirements for plastic collapsible containers used as blood bags. This standard specifies the material properties, design features, and performance criteria necessary to ensure the safe collection, storage, and transfusion of blood.
WHO Guidelines on Blood Safety
Until now, scant references on improving blood safety worldwide exist —this is the rationale behind WHO’s recently released Integrated approach to blood safety and availability. They also stress the need to use high-quality materials and to use layers of testing protocol. It includes also the ethical considerations surrounding blood donation and the need for solid systems for blood product traceability. Following WHO guidelines helps manufacturers like Medco to keep the trust of people as well as safe 500 ml blood bags are for use.
National Regulations and Compliance
While international standards provide a framework, national regulations offer specific directives that manufacturers must follow within different jurisdictions.
FDA Regulations in the United States
In the U.S., the Food and Drug Administration (FDA) regulates medical devices under the Federal Food, Drug, and Cosmetic Act. Blood bags are Class II medical devices requiring premarket notification or 510(k) clearance to market. FDA requires stringent evaluation of biocompatibility, sterility, and shelf-life stability.
European Union Directives
The Medical Device Regulation (MDR) lays out the respective directives which govern Medical devices in the European Union. To prove alignment with fundamental health and safety standards, this regulation requires manufacturers to perform both clinical evaluations and risk assessments. CE marking is required for all medical devices within the member states of the EU which demonstrates conformity with the MDR requirements.
Best Practices for Handling 500 ml Blood Bags
Ensuring the safe handling of 500 ml blood bags is as important as complying with regulatory standards. Proper techniques minimize risks during storage and transportation.
Proper Storage Techniques
Effective storage practices are vital in preserving the quality of blood products.
Temperature Control Measures
Blood bags should be stocked at regulated temperatures so that they cannot be spoiled. Refrigeration between 2°C to 6°C stability for red cells is advisable. Deploy the temperature monitoring system to detect temperature changes that would compromise product integrity.
Avoiding Physical Damage to Bags
Physical damage can lead to contamination or leakage, posing significant risks. It’s essential to handle blood bags with care, avoiding sharp objects or excessive pressure during storage. Implementing protective measures such as cushioned shelving can mitigate potential damage.
Safe Transportation Methods
Transporting blood products requires meticulous planning to ensure they reach their destination safely.
Ensuring Secure Packaging
Secure packaging is critical in protecting blood bags from physical harm during transit. Using insulated containers with shock-absorbing materials can safeguard against temperature variations and mechanical impacts.
Monitoring During Transit
Continuous monitoring during transportation helps maintain optimal conditions for blood products. Employing data loggers that record temperature changes ensures immediate corrective actions if deviations occur. This proactive approach minimizes risks associated with long-distance shipping.
When implemented and embraced by manufacturers like Medco, these best practices serve as strong pillars of product safety while reinforcing compliance with internationally recognized standards and national regulations. Right from production to distribution, high-quality products are the mobile of Medco to maintain its status as a credible medical supply company worldwide.
Quality Assurance in Blood Bag Manufacturing
Material and Design Considerations
Use of Biocompatible Materials
Materials selection is one of the most important aspects of 500 ml blood bag manufacturing. The materials are biocompatible, meaning that they do not trigger a negative reaction (meaning they are okay in human blood). Manufacturers have to select polymers that are non-reactive and have no leachable material that may contaminate the blood. High-grade medical polyvinyl chloride, often DEHP- or other plasticizer-based, is used in many instances due to its historical safety profile and pliable nature. Medco, which is one of the biggest manufacturers, performs extensive testing of its materials to guarantee they are biocompatible, and thus, its blood bags are suitable for clinical use.
Design Features for Safety and Efficiency
Designing the bag has a major influence on end-user experience as well as patient safety. Leak-proof seals, strong ports for making fast and secure connections, and clear labels for traceability are standard features. The ergonomically created bag shapes and port flow (easy plug-in) align with the blood collection and transfusion work practices and increase operational efficiency. Medco considers incorporating these features in design solutions to meet both functionality and safety in the 500 ml blood bags.
Testing and Validation Processes
Rigorous Testing Protocols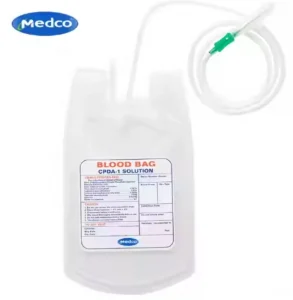
500 ml blood bag manufacturers need stringent testing protocols at every stage of production to maintain the highest level of quality. They include physical integrity, sterility assurance levels (SAL), and chemical composition tests among others. All batches are thoroughly tested for ISO conformity and FDA compliance. Medco leverages advanced testing technologies to catch possible flaws in the early stages of the manufacturing process minimizing the likelihood of product failure.
Continuous Monitoring for Defects
Constant checking is required to control the quality at all stages of production. They can help track things such as temperature, pressure, and humidity during manufacture using automated systems. In case there are any anomalies and there is a deviation from set standards then immediate corrective action can be taken owing to real-time data collection. Medco, which is constantly seeking to improve, has invested in modern monitoring systems that promote product quality.
Medco’s Role in Enhancing Blood Safety
Medco’s Commitment to Quality Products
Medco has built a reputation in the medical device sector for providing quality products that comply with regulations. A comprehensive quality management system (QMS) that regulates all stages of production — starting from the selection of materials, and finishing with delivery of the ready-made products — is a sign of the company’s commitment to quality. Medco’s commitment to excellence in manufacturing is evident by strict compliance with international standards like ISO 13485.
Overview of Medco’s Medical Devices and Solutions
Medco has an extensive portfolio of medical devices for different healthcare specialties available for market access to facilitate better patient management. Besides blood bags, their portfolio covers infusion systems, diagnostic equipments, and surgical instruments with a focus on precision and reliability. Medco aims to bring continuous innovation in collaboration with healthcare professionals across the globe and develop solutions to the newest challenges that can be faced in medical technology whilst ensuring patient safety all the time.
Ultimately, thorough compliance to established regulations, along with well-planned quality assurance methods, is the key to success for 500 ml blood bag manufacturers, such as Medco. Using biocompatible materials, smart design features, comprehensive testing procedures, and advanced surveillance technologies, manufacturers would be able to bring their products up to the standards of safety—strengthening global health in the process.